BRIGHT ABRASIVES · Septiembre 23, 2022
La mayoría de las industrias han adoptado procesos de mecanizado (de introducción de máquinas para incrementar la productividad) que mejoran tanto el diseño como la implementación de técnicas de control efectivas para optimizar las operaciones de corte (1). Estos procesos utilizan diversas técnicas como el fresado, el grabado, el torneado y el taladrado para lograrlo.
De todos los anteriores, el taladrado es el mejor método para mecanizar agujeros, es decir, para crear agujeros a gran velocidad, con una buena profundidad, con precisión extraordinaria y en todo tipo de materiales. Esta técnica es posible gracias a diversas herramientas de corte llamadas puntas para taladro o brocas.
Por esta razón, en este artículo te contamos qué son las puntas para taladro, cuáles son sus partes y qué tipos hay.
Taladrado
El taladrado es un proceso cuyo objetivo es crear agujeros que se producen por el arranque de viruta (residuos del material) por medio de la rotación de una punta que recibe el nombre de punta para taladro o broca.
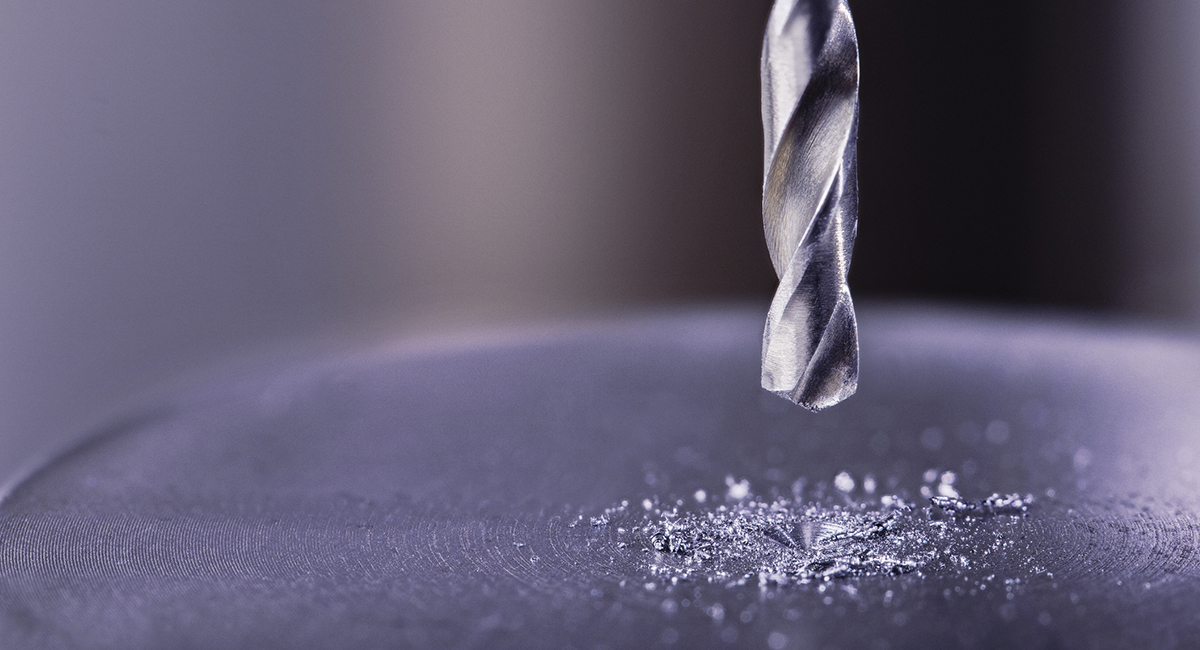
Para realizar este proceso es necesario tener herramientas eléctricas que se conforman de una carcasa de plástico, de un gatillo que permite echarlo a andar y de un mandril (pieza de forma cilíndrica en que se asegura algo que se ha de tornear) que, a su vez, requiere de la punta o broca.
Taladrar exige un movimiento de rotación. El procedimiento más antiguo para lograrlo se conoce como “arco de violín” (2).
En Bright Abrasives fabricamos, convertimos y distribuimos material abrasivo y herramientas para pulir. Conoce nuestro catálogo completo, que incluye diversos tipos de taladros, como con gatillo (para iniciar el taladro neumático) y reversibles de aire.
Puntas de pulido para taladro
Las puntas para taladro (también llamadas brocas) son herramientas de corte diseñadas y fabricadas para expeler material al mismo tiempo que crean cavidades cilíndricas en éste. En palabras más sencillas, podemos decir que estas puntas son objetos alargados que crean agujeros en un material.
En la actualidad, existe una diversidad muy grande de puntas para taladro. Hay puntas con diferentes formas, materiales y tamaños que producen cavidades con características muy diversas en una amplia gama de superficies.
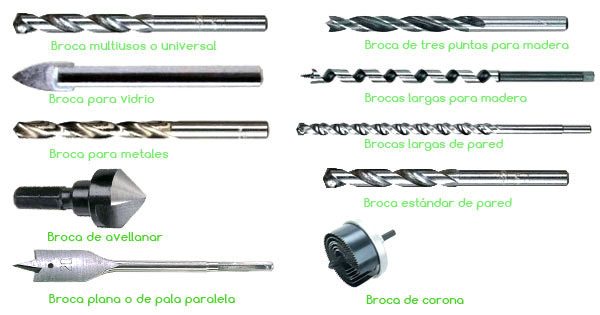
Sus características están condicionadas según la finalidad para la que hayan sido elaboradas. Para determinar dicha finalidad se toman en cuenta, principalmente, la dureza del material en la que van a crear las cavidades o agujeros y la velocidad con la que es necesario eliminar este material.
Para funcionar, las puntas para taladro necesitan acoplarse a taladros u otros instrumentos que son los que producen el empuje y la potencia requeridos para hacer los agujeros.
Las pastas abrasivas son materiales que se aplican sobre diversas herramientas para modificar una superficie. Lee sobre sus aplicaciones abrillantadoras y de pulido en este enlace.
Partes
Las puntas para taladro pueden conformarse de diversas partes; sin embargo, hay algunas que son comunes en la mayoría de éstas (2) (3):
1. Diámetro del vástago. Medida que determina la anchura del vástago (barra metálica que, en este caso, une la punta con el taladro).
2. Longitud del vástago. Medida que establece el largo del vástago. Es el extremo que está sujeto por el taladro.
El vástago es cilíndrico para diámetros menores a 13 milímetros y cónico para diámetros mayores a esta medida (2).
3. Longitud del canal. Medida que da cuenta el largo de la parte cortante de la punta para taladro. Representa la profundidad máxima que se puede taladrar. También es llamada “longitud de corte”.
4. Longitud total. Medida que precisa el largo de toda la punta para taladro. Empieza con el extremo final del vástago y llega hasta el final del canal. De acuerdo con esta longitud, hay puntas para taladro normales, largas y súper largas.

5. Ángulo de la punta. Medida en grados que forman los bordes del canal. Los ángulos principales son el de ángulo de corte de 118° y el de ángulo de corte de 135°.
El de 118 ° es para uso general y es el más popular, no tiene centrado automático, es más usual en taladros estacionarios y presenta un mejor rendimiento en materiales suaves que en metales duros. En cambio, el de 135° es menos conocido, exige menos fuerza que el anterior, no resbala, ofrece centrado automático y es más utilizado en taladros portátiles.
Además de éstos, también existe el ángulo turbo que ofrece afilación más duradera, centrado automático, perforación más rápida y precisión rectificada. Al igual que el de ángulo de 135° funciona mejor con taladros portátiles y requiere menos fuerza que el de 118°.
6. Diámetro de la punta. Medida que refiere a la anchura de la cavidad que forma. Hay diámetros estandarizados; sin embargo, también se pueden elaborar puntas con diámetros personalizados según las necesidades de cada cliente.
Algunos fabricantes también consideran como partes esenciales los labios o flautas (los bordes exteriores), tanto su cantidad como en su profundidad, y el ángulo de la hélice cuyo objetivo es posibilitar la expulsión de la viruta (2).
En Bright Abrasives tenemos los mejores productos para tus piezas de aluminio, acero inoxidable, titanio y otros metales, entre ellos taladros neumáticos de cojín y taladros reversibles de aire. Contáctanos para recibir más información sobre nuestras herramientas para pulir, nuestras ruedas de pulido y nuestras pastas abrasivas.
Clasificación de puntas de pulido para taladro
Las puntas para taladro pueden clasificarse de acuerdo con diferentes criterios como son el material del cuál están hechas, el material de la superficie sobre la cual van a crear los agujeros, la profundidad del agujero que producen, la forma o el ángulo de punta que tienen, el tipo de corte que logran, las condiciones de dicho corte, tipo de mango, entre otras (1).
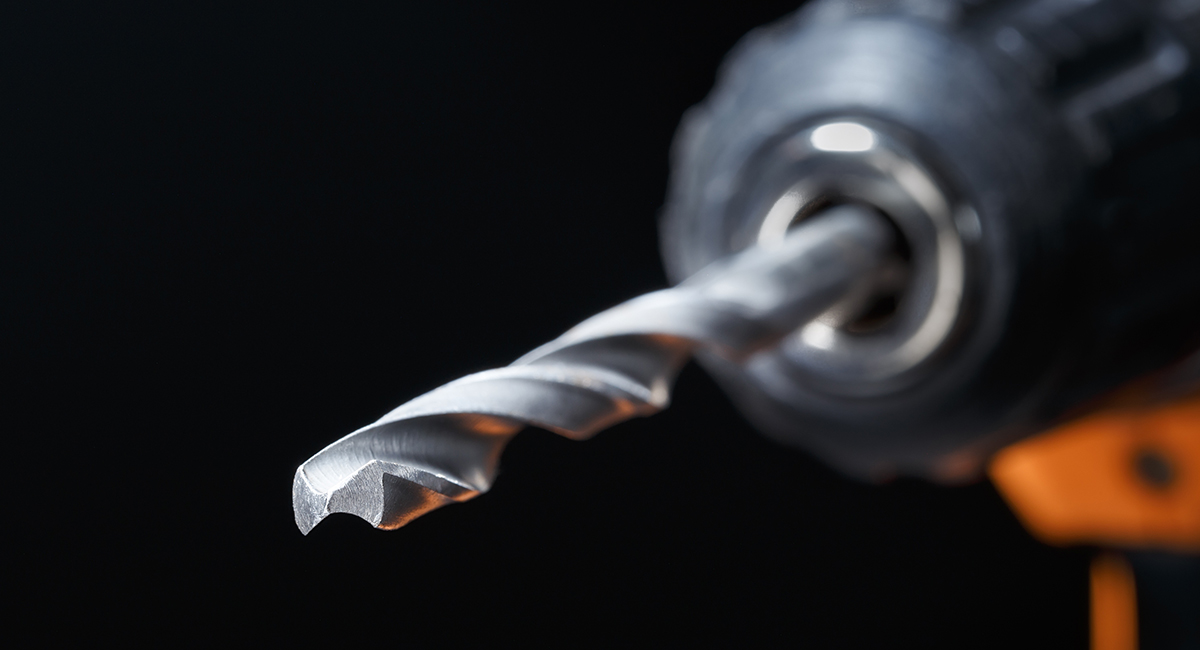
los avellanadores para achaflanar y los escariadores para crear cavidades con tolerancia estrecha.
En Bright Abrasives queremos compartir contigo tres clasificaciones por parecernos las más representativas. La primera tiene como criterio el material constitutivo de la punta para taladro; la segunda, la finalidad que cumplen las puntas para taladro; y la tercera, el material sobre el cual se crean las cavidades.
Material constitutivo
Las puntas de taladro se elaboran, casi en su totalidad, con tres tipos de materiales (2):
- Acero al carbono. Están hechas con acero, en el que la proporción de cualquiera de sus elementos aleantes (ya sea cromo, manganeso, níquel, silicio, titanio o vanadio) es menor que la de carbono. Se prefieren para taladrar materiales blandos como madera o plástico.
- Acero rápido. Fabricadas con aceros de alta velocidad o high speed steel (HSS) en cuya composición intervienen elementos como el molibdeno, el vanadio y el wolframio. Son la mejor opción para el proceso de taladrado de aceros de poca dureza.
- Metal duro. Elaboradas con un compuesto de partículas de carburo de tungsteno y un aglomerante saturado de cobalto metálico (4). Representan una gran opción para trabajar aceros de gran rendimiento y fundiciones.
A estos materiales puede agregárseles un recubrimiento, parcial o totalmente, de otros materiales como níquel, óxido negro o titanio para dotarlas de otras características (2).
El funcionamiento de los discos abrasivos depende del sistema al que se unan: sistemas de platos de soporte o sistemas orbitales. Entérate de las características de cada uno aquí.
Finalidad
De acuerdo con el propósito que cumplen, las puntas de taladro pueden clasificarse en (1):
- De centros. Corta y produce cavidades cilíndricas en el extremo final de una pieza de material por lo que puede montarse entre los centros del cabezal y el cabezal móvil o contrapunto de un torno.
- Punta de cruz para taladro. Aprietan o aflojan tornillos, por lo que simplifican tareas de reparación y ajuste. A diferencia de las anteriores y las que la anteceden, éstas no crean cavidades o agujeros.
- De núcleo. Agranda cavidades previamente existentes. También llamada “punta para taladro de sondeo” o, simplemente, “punta de sondeo”.
La invención del acero rápido en 1898 impactó de manera positiva en el aumento de la velocidad de los taladros (2).
- De paleta. Produce cavidades de gran profundidad y diámetro ancho. Además, se caracterizan por tener barrenas removibles. Recibe los nombres de “punta para taladro tipo espada” o “punta tipo espada”.
- Escalonada. Genera cavidades con dos o más diámetros de diferente anchura.
- Helicoidal. Ofrece la generación de cavidades sólidas para usos estándar. Crea agujeros donde quedan combinados tanto cortes activos como centrados perfectos.
Es usual que todas estas puntas se agrupen y formen un juego de puntas para taladros. Estos conjuntos pueden estar formados por puntas o brocas de diferentes tipos o que pertenezcan a uno mismo pero sean distintas en ángulo de punta, longitud, espesor u otro rasgo.
Material perforado
Según el material que las puntas de taladro perforen, éstas pueden crear cavidades cilíndricas en (5) (6):
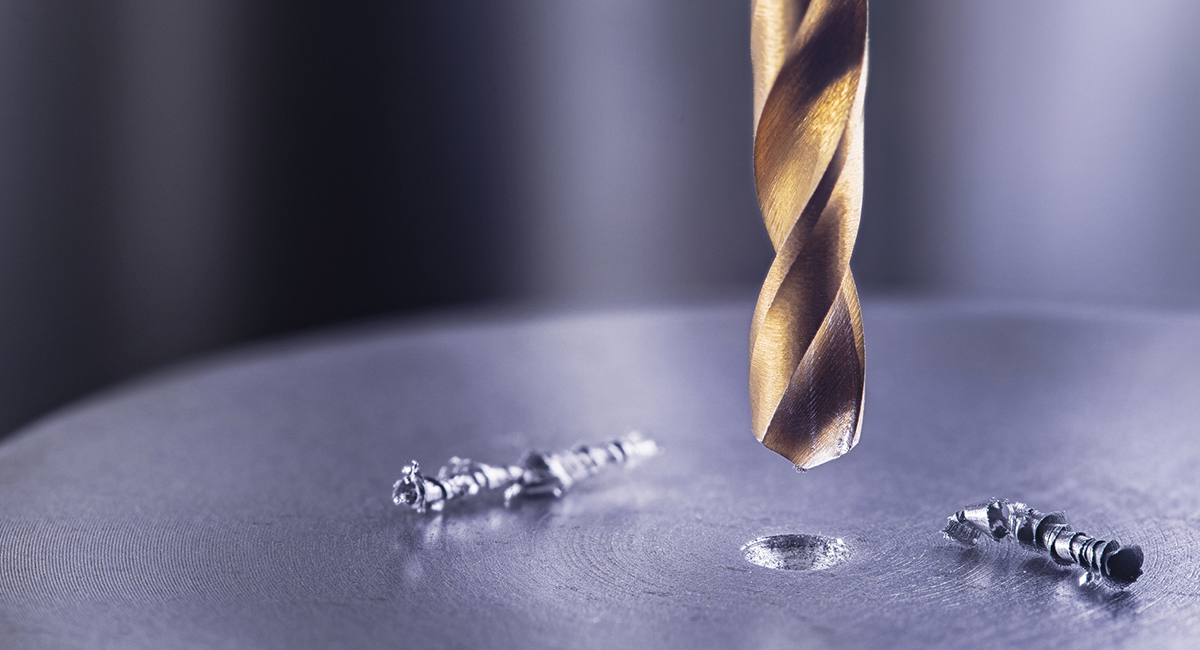
En todas sus aplicaciones es deseable la maestría de los operadores para evitar cualquier accidente.
- Acero. Para materiales de aleación de hierro y carbono con otros elementos (cobalto, molibdeno, níquel, tungsteno) en proporciones variables. Se caracterizan por ser materiales de viruta larga pero con un control de ésta relativamente sencillo y uniforme.
- Acero inoxidable. Para materiales de aleación de hierro y carbono con un proporción mínima del 10 al 12 % de cromo contenido en masa. El acero inoxidable produce viruta larga y el control de ésta es regular en el ferrítico y más complejo en el austenítico y en el dúplex.
- Fundición. Para materiales creados por la operación que consiste en derretir un metal sólido por la acción del calor. Son materiales de viruta corta y permiten un buen control de ésta en todas las condiciones.
- Aleación especial. Para materiales que resultan de la mezcla sólida o líquida de metal con metal, metal con elemento no metálico o varias porciones de un mismo metal. Normalmente son a base de cobalto, hierro, níquel y titanio. Sus características principales son que poseen una viruta larga y que su control resulta complicado.
Escoger la punta de taladro adecuada garantiza, en buena medida, el éxito de un proceso de taladrado.
- Metal no férrico. Para materiales que en su fabricación no interviene el hierro en cantidades considerables. Algunos de los metales no férricos o no ferrosos son el aluminio, el cobre, el estaño, el plomo, el titanio y el zinc; los metales como el oro, la plata y algunas aleaciones como el latón. Tienen viruta larga y su control es sencillo siempre que sean aleados.
- Material endurecido. Para materiales que pasaron por un proceso para incrementar su dureza. Son materiales de viruta larga y su control es mayormente regular.
Usualmente, los fabricantes de puntas para taladros crean códigos en los que indican, entre otras características, este material.
A cada material le corresponde una letra, un número o una combinación de éstos que permite identificarlas. Cada fabricante elige un símbolo alfanumérico distinto.
En Bright Abrasives te ofrecemos también servicios de entrenamiento (capacitamos a tu equipo técnico para que aprovechen al máximo nuestros productos), de consultoría (evaluamos para ofrecerte una ruta de mejora) y de soporte (ponemos a tu disposición a nuestros especialistas). ¡Ponte en contacto con nosotros ahora y adquiere alto rendimiento, calidad, durabilidad y versatilidad!
La calidad del proceso de lijado depende casi en su totalidad del tamaño del grano utilizado. Revisa los usos que se le dan a cada grano en este artículo que preparamos para ti.
Referencias
- Pablo Borrell. Análisis de fuerzas de corte en procesos de taladrado para aluminio 2024 T6. Universidad Nacional Autónoma de México, 2017. Consultado el 16 de mayo de 2022.
- Acomee. Taladradora. Acomee, s/f. Consultado el 16 de mayo de 2022.
- Irwin. Perforación de metal. Irwin, s/f. Consultado el 16 de mayo de 2022.
- Instituto Azteco. ¿Qué es el metal duro? Instituto Azteco, 2021. Consultado el 17 de mayo de 2022.
- Mitsubishi. Herramientas para taladro. Mitsubishi, s/f. Consultado el 16 de mayo de 2022.
- De máquinas y herramientas. Materiales según la norma ISO. De máquinas y herramientas, 2015. Consultado el 17 de mayo de 2022.
Deja una respuesta